Fluid Transfer: Moving fluids from one location to another, such as in water supply and fuel transfer.
Pressure Boosting: Increasing the pressure of fluids to meet specific system requirements, commonly found in water supply systems and hydraulic applications.
Circulation: Continuously circulating fluids within systems, like cooling or heating circuits.
Dosing: Precisely metering and controlling fluid flow, particularly in chemical processes.
Types of Pumps
Centrifugal Pumps
Description: The most commonly used type of pump, centrifugal pumps harness rotational kinetic energy from an impeller to move fluids.
Applications: Used in water supply, wastewater treatment, oil refineries, power plants, and irrigation.
Key Parts:
- Impeller: The rotating component that imparts velocity to the fluid.
- Casing: The outer shell that encases the impeller and directs fluid flow.
- Shaft: Connects the impeller to the motor or turbine.
- Mechanical Seals: Prevent fluid leakage along the rotating shaft.
Types of Centrifugal Pumps:
- Axial Flow Pumps: Push fluid parallel to the pump shaft.
- Radial Flow Pumps: Direct fluid perpendicular to the pump shaft.
- Mixed Flow Pumps: Combine axial and radial flow characteristics.
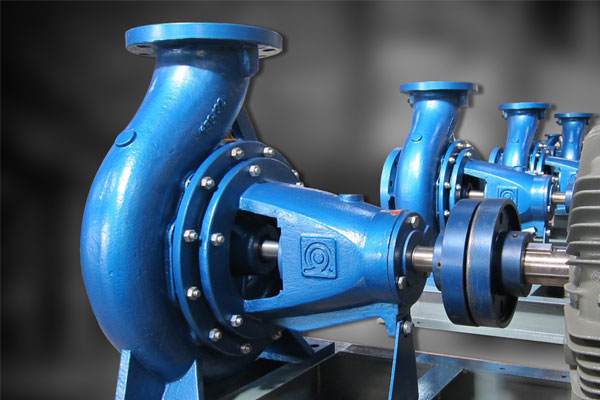
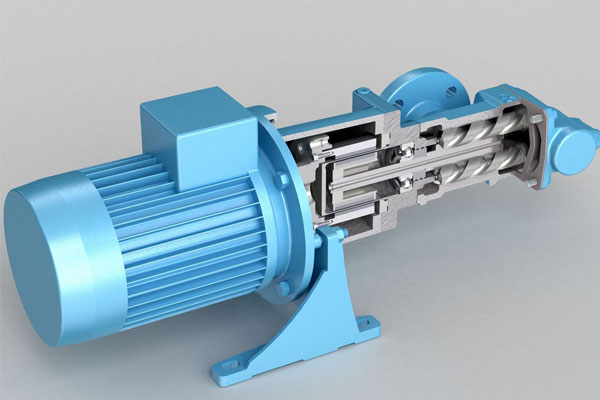
Positive Displacement Pumps
Description: These pumps move fluids by trapping a fixed amount and forcing (displacing) it through the system, maintaining a consistent flow regardless of system pressure.
Applications: Ideal for high-pressure applications, chemical dosing, hydraulic systems, and fuel injection.
Key Parts:
- Rotors or Pistons: Mechanically displace fluid.
- Chambers: Enclosed spaces that trap fluid and push it through the system.
Types of Positive Displacement Pumps:
- Rotary Pumps: Use rotating parts to move fluids, such as gears or lobes (e.g., gear pumps, lobe pumps).
- Reciprocating Pumps: Use a piston or diaphragm to push fluids back and forth (e.g., piston pumps, diaphragm pumps).
- Peristaltic Pumps: Utilize rollers to compress a flexible tube, thereby pushing fluid through it.
Diaphragm Pumps
Description: These pumps employ a flexible diaphragm that moves back and forth to create suction and discharge.
Applications: Commonly used in chemical processing, food and beverage production, wastewater treatment, and applications handling corrosive fluids or slurries.
Key Parts:
- Diaphragm: A flexible membrane that displaces fluid.
- Check Valves: Ensure one-way fluid flow through the pump.
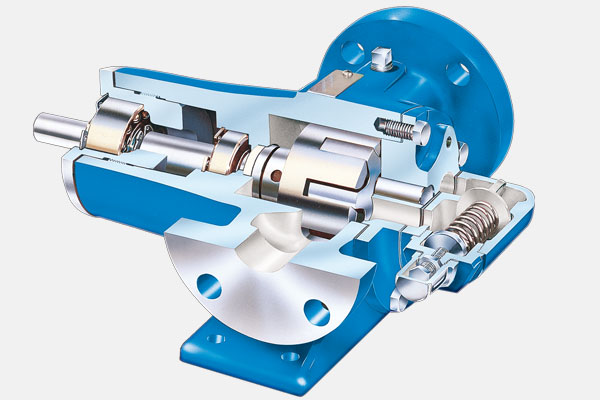
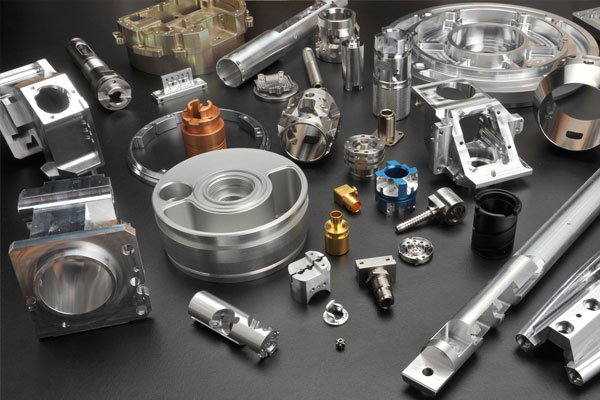
Gear Pumps
Description: A type of positive displacement pump that moves fluid through the action of meshing gears.
Applications: Used for oil transfer, chemical processing, and hydraulic fluid transfer.
Key Parts:
- Gears: Rotate to propel fluid through the pump.
- Casing: Encloses the gears and directs fluid flow.
- Shafts: Drive the rotation of the gears.
Peristaltic Pumps
Description: Also known as hose pumps, these pumps operate by compressing and releasing a flexible tube to move fluid.
Applications: Used in laboratories, for chemical dosing, in pharmaceuticals, and in the food and beverage industries.
Key Parts:
- Flexible Tube or Hose: The pathway through which the fluid flows.
- Rollers or Shoes: Squeeze the hose to propel fluid.
- Drive Mechanism: Rotates the rollers or shoes.
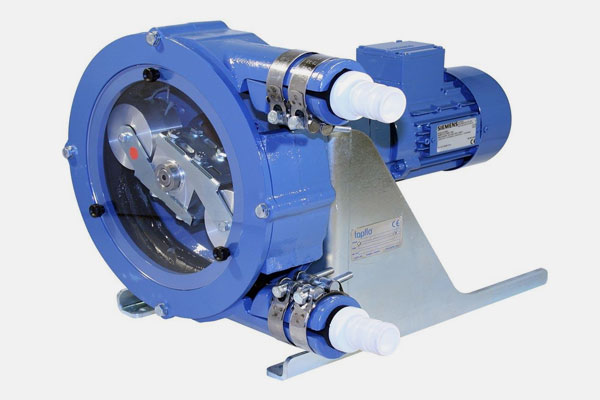
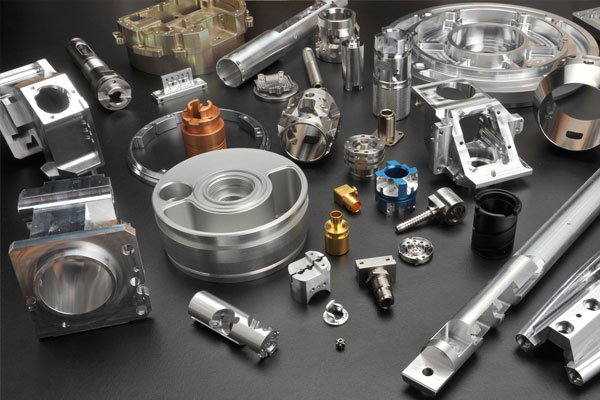
Submersible Pumps
Description: Designed to function while fully submerged in the fluid they are pumping.
Applications: Commonly used in water wells, drainage systems, sewage systems, and deepwater pumping.
Key Parts:
- Motor: Housed in a waterproof casing.
- Impeller or Propeller: Drives the movement of fluid.
- Seals: Prevent fluid from entering the motor compartment.
Vacuum Pumps
Description: Remove air or gas molecules from a sealed volume to create a vacuum.
Applications: Employed in vacuum systems, HVAC systems, laboratories, chemical processing, and food packaging.
Key Parts:
- Rotors or Vanes: Mechanisms that trap air or gas and expel it from the system.
- Chamber: The enclosed space from which air or gas is extracted.
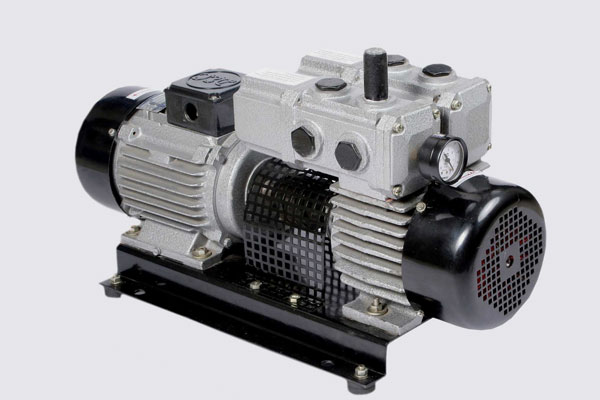
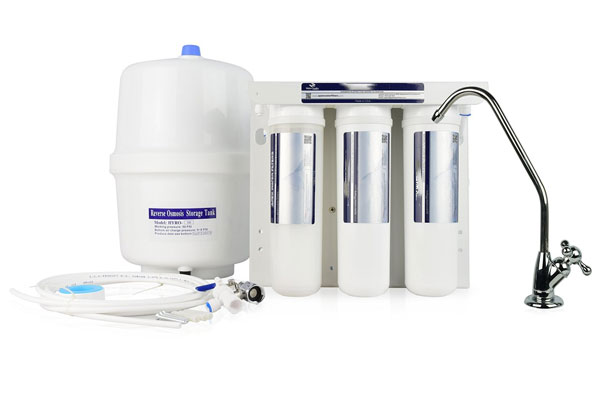
Permeate Pumps (Reverse Osmosis)
Description: Enhance the efficiency of reverse osmosis (RO) water systems by reducing back pressure and maximizing water flow.
Applications: Primarily used in water purification systems, especially in RO setups.
Key Parts:
- Piston or Diaphragm: Moves water through the reverse osmosis membrane.
- Check Valves: Maintain the direction of water flow.
Vacuum Pumps
Description: Remove air or gas molecules from a sealed volume to create a vacuum.
Applications: Employed in vacuum systems, HVAC systems, laboratories, chemical processing, and food packaging.
Key Parts:
- Rotors or Vanes: Mechanisms that trap air or gas and expel it from the system.
- Chamber: The enclosed space from which air or gas is extracted.
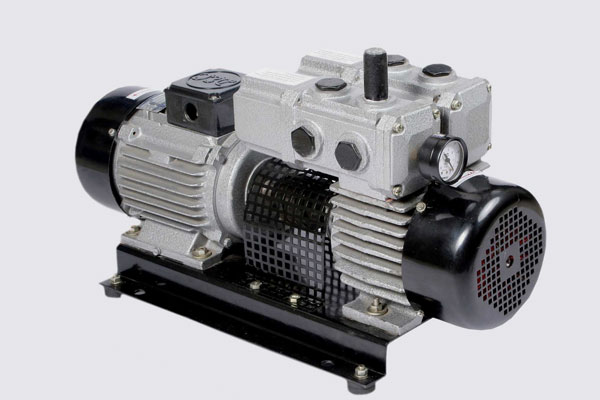
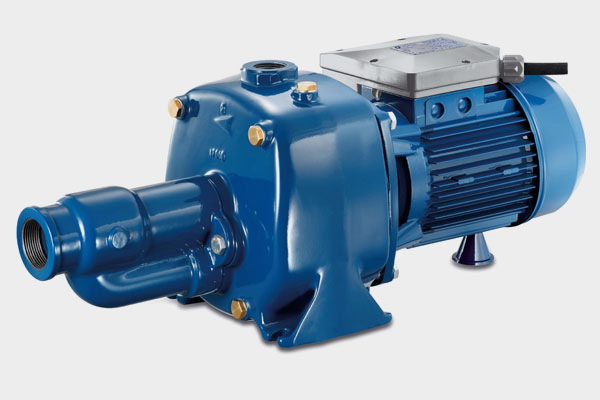
Jet Pumps
Description: Utilize a jet of fluid to create a low-pressure area that draws fluid from a well or reservoir.
Applications: Suitable for shallow wells, water supply, and irrigation.
Key Parts:
- Nozzle: Directs a fluid jet to create suction.
- Venturi: A tube that narrows to increase fluid speed and reduce pressure.
Multistage Pumps
Description: Comprise multiple impellers arranged in series to progressively increase fluid pressure at each stage.
Applications: Used in high-pressure applications, boiler feed, and water injection in oil fields.
Key Parts:
- Impellers: Several stages of impellers that increase pressure step by step.
- Casing: Contains all impellers and directs fluid flow.
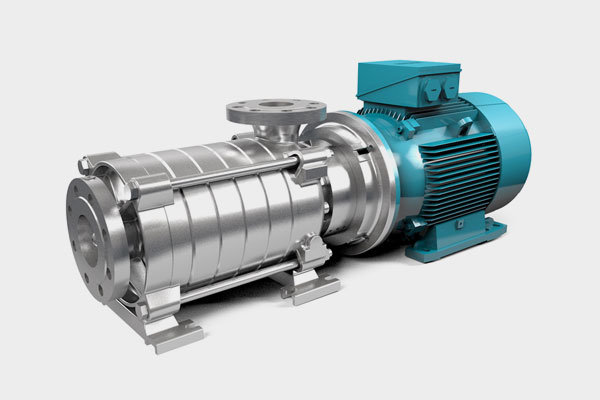
Common Pump Materials
Depending on the application and the type of fluid being handled, pumps are constructed from various materials, including:
- Cast Iron: Commonly used in water and low-corrosive applications.
- Stainless Steel: Frequently found in food processing, pharmaceuticals, and chemical applications due to its resistance to corrosion.
- Bronze: Often selected for marine applications due to its corrosion resistance in saltwater environments.
- Plastic (PVC, Polypropylene, etc.): Ideal for lightweight, corrosion-resistant applications, particularly in chemical handling.
- Ceramic or Hard Metal Liners: Commonly used in slurry pumps to withstand wear from abrasive materials.
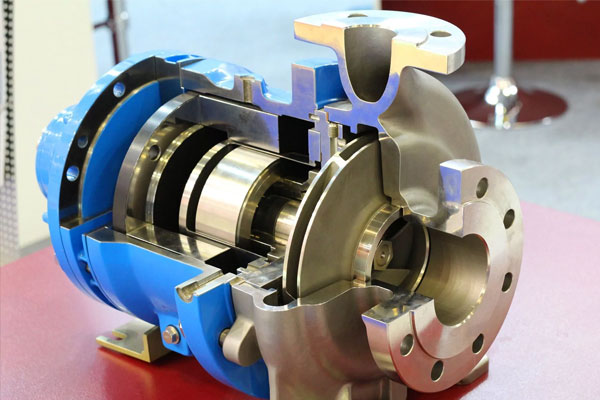
Pump Applications
Pumps are utilized across various industries, with each type engineered to meet specific requirements, including:
- Oil & Gas: For crude oil transfer, water injection, and refining processes.
- Water & Wastewater: In water supply systems, sewage handling, and irrigation.
- Chemical Processing: For handling corrosive and hazardous fluids.
- HVAC Systems: To circulate heating or cooling fluids.
- Mining: For dewatering mines and slurry handling.
- Power Generation: To circulate cooling water, boiler feed water, and transfer fuel.
- Food & Beverage: Sanitary pumps for handling milk, juices, and other fluids.
- Pharmaceuticals: For precise dosing of chemicals and handling sensitive fluids.
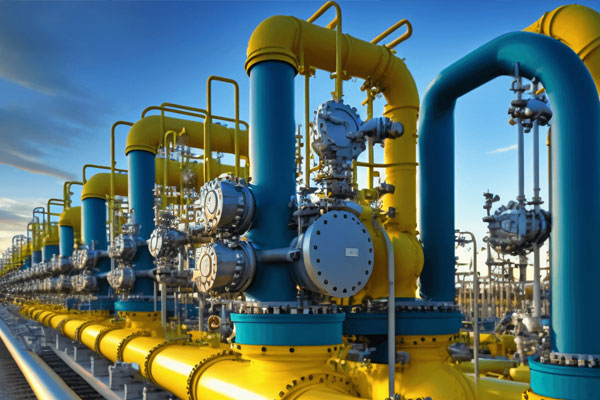
Pump Performance Considerations
When selecting a pump, it is essential to consider several factors to ensure optimal performance:
- Flow Rate (Capacity): The volume of fluid a pump can move over time, typically measured in gallons per minute (GPM) or liters per minute (LPM).
- Head (Pressure): The height to which a pump can raise fluid, usually measured in meters or feet.
- Viscosity: The thickness of the fluid being pumped, influencing the type of pump used.
- Corrosion Resistance: Choosing materials that can withstand the chemical nature of the fluid.
- Temperature: Ensuring the pump can manage the operating temperature of the fluid.
- Efficiency: Selecting an energy-efficient pump for long-term use, especially in continuous operations.
Pumps are integral to many industrial and residential systems, and their proper selection, installation, and maintenance are crucial for ensuring operational efficiency and reliability.
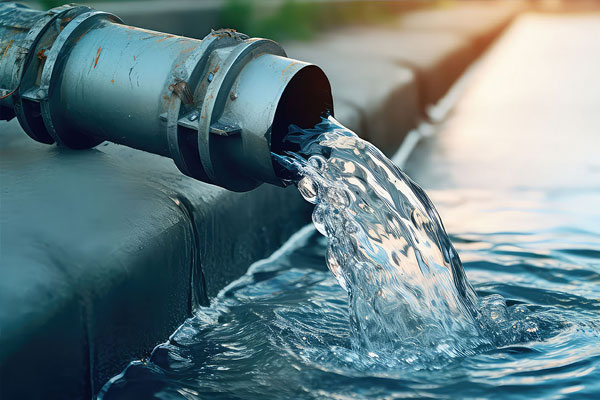